When the ground shifts, a building’s true strength is tested. Traditional braces often hold the line but fall short of offering long-term safety and adaptability. The challenge is clear: we need systems that absorb and adapt under pressure and easily integrate with other systems in the building.
That’s where buckling restrained braced frames (BRBFs) come in. These seismic innovations do more than resist; they set a new standard for structural protection.
Let’s explore how BRBFs are reshaping the future of seismic safety.
How Do Buckling Restrained Brace Frames Work?
First, let’s dive into the mechanics of buckling restrained brace frames. BRBFs manage seismic forces more effectively than conventional bracing systems, making them essential in earthquake-prone areas.
What Makes BRBFs Different from Conventional Braces?
Conventional braces carry loads primarily in tension, but under compression, they risk buckling—like crumpling paper. Once they buckle, they are ineffective. This can lead to uneven force distribution and structural damage during an earthquake.
This is where BRBFs step in as the superior option.
Their standout feature?
They handle both tension and compression forces with ease. The core of the BRBF is designed to yield—absorbing seismic energy while maintaining its integrity—without buckling. It works as a shock absorber for your building, dissipating earthquake forces and protecting the structure’s critical elements like columns, beams, and foundations.
Key Features That Make BRBFs a Game-Changer
Let’s break down what sets BRBFs apart:
- The Yielding Core: The steel core dissipates energy by yielding under tension. It functions as a fuse, designed to prevent exceeding the capacity of the connections and structural members.
- Buckling Resistance: Surrounding the core is a stabilizing system that prevents it from buckling. This allows the brace to handle compression forces, unlike conventional systems.
- Efficiency in Design: With BRBFs many design configurations are available to meet architectural needs. You can replace an X-brace configuration with a single diagonal brace, simplifying the structure while maintaining structural soundness.
- Precision Manufacturing: At EVER Seismic, we use an all-steel design instead of concrete-filled braces. Why? It’s lighter, fully recyclable, and—bonus—fits into narrower spaces. (But more on this later.)
Top BRBF Applications Across Industries
From iconic high-rises, retrofitting historical structures and industrial buildings, BRBFs prove their worth all around the world:
- L.A. Stadium, USA: This massive structure relies on BRBFs to remain resilient in a seismically active region.
- Salt Lake City Airport, USA: BRBFs provide cost-effective earthquake protection without compromising on design or functionality.
- Renaissance Tower, Turkey: In one of the most earthquake-prone regions in the world, BRBFs play a crucial role in ensuring structural safety.
Here you can find more examples of BRBF applications, or you can explore AISC’s case studies.
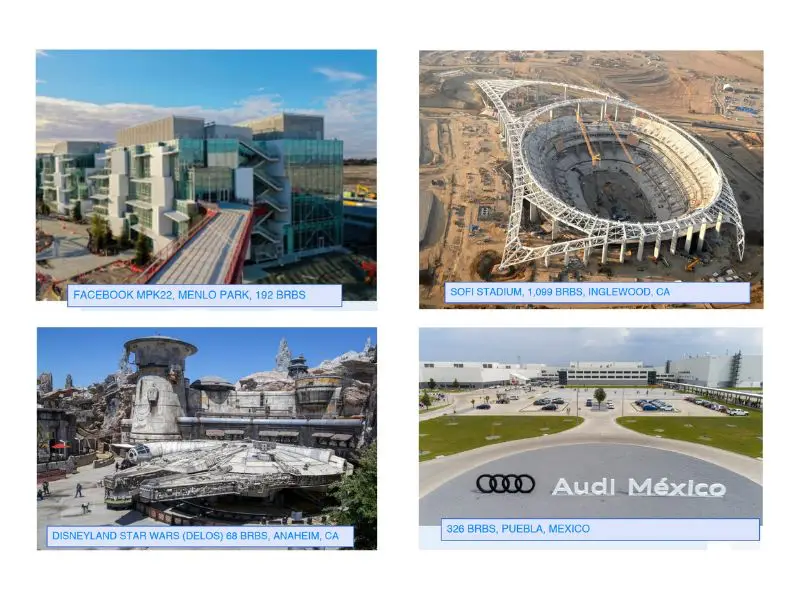
Buildings using buckling restrained braces
Key components – Buckling Restrained Braced Frame Parts
To truly appreciate the ingenuity of buckling restrained braced frames, it helps to understand how the different parts work together like a well-oiled machine. Every component plays a specific role in stabilizing the structure, especially under seismic stress. Let’s break it down—piece by piece.
- The Core: The Heart of the System
At the center of every buckling restrained brace lies the steel core. This is the part that directly connects to the beams and columns of the structure.
Its job?
To yield in both tension and compression during an earthquake, absorbing seismic energy to protect the rest of the building.
- The Restraining Mechanism: Buckling Control
Surrounding the core is a restraining mechanism that keeps it from buckling under pressure. This can take different forms:
- Concrete-filled steel casings: Traditionally used to stabilize the core.
- All-steel designs: Our innovation, that we manufacture at EVER Seismic. Our steel plates provide the same level of restraint without the added weight and recycling challenges of concrete.
- Connections: The Crucial Link
BRBs can use bolted, welded, or pin connections to attach to the gusset. A reliable connection ensures the brace functions as designed, transferring the strain-hardened loads while stabilizing the gusset plate.
At EVER Seismic, we start with bolted connections because they’re simpler to install and cost-effective without compromising on performance. However, we can customize connections to fit your needs.
- Gusset Plates: The Load Transfer Specialist
Gusset plates connect the brace to the building’s columns and beams. These are like the intermediaries that ensure loads are effectively transferred between the brace and the structure. EVER Seismic does all of the gusset design where it interfaces with the BRBs.
All-Steel BRBF’s – The Future of Buckling Restrained Bracing
Although BRBFs are superior on their own compared to traditional seismic bracing technologies, at EVER Seismic we took things up a notch.
How?
We created an all-steel buckling restrained brace, called EVER Brace, the next evolution in seismic technology. Combining “Strain Control Technology,” precision manufacturing, and built-in “Holistic Gusset Stability” Technology, this innovative brace redefines what’s possible in structural resilience.
How All-Steel Braces Stand Out
The “traditional” BRBFs feature a steel core encased in a steel tube, which is then filled with concrete. The concrete prevents the steel core from buckling while allowing it to yield under tension and compression.
While this is a time-tested design with wide industry adoption, this solution has a lot of challenges: heavier weight, non-recyclable materials, and potential quality control issues during concrete filling and curing.
So we’ve taken BRBF design to the next level with an all-steel brace.
Why? Because it’s:
- Lighter: Half the weight of conventional concrete-filled designs. This doesn’t just reduce the load on the building—it impacts the entire construction process. A lighter brace means a smaller crane, simplifying logistics and cutting costs.
- More Sustainable: Fully recyclable, unlike concrete-filled braces that require labor-intensive material separation.
- Slimmer: The assembly process is different allowing narrower casings. It can fit. into narrower spaces, giving architects more design flexibility.
- Easier to Install: Thanks to our holistic approach to connection design, our braces slide effortlessly into place from the side by slotting the gusset plates, then bolt up securely—streamlining on-site assembly and cutting down on time and labor costs.
What Makes the EVER Brace Even More Different?
At EVER Seismic, we’ve tackled the toughest challenges in manufacturing and the everyday realities of construction to create a seismic brace that rises above them all. It’s not magic—it’s science, math, and expertise coming together to deliver innovation you can rely on.
Strain Control Technology: Taking Performance Further
Where traditional braces meet the 3% performance standard, the EVER Brace goes above and beyond.
With its advanced displacement control system, it can withstand the standard testing protocol up to 3% strain then 11 Northridge-level earthquakes before showing signs of failure. This technology engages the entire length of the steel core, delivering durability like never before.
Holistic Gusset Stability: Stability Where It Counts
We’ve flipped the script on gusset stability.
Instead of relying on the gusset to stabilize the brace, the EVER Brace is designed to stabilize the gusset.
This built-in stability ensures better performance for the entire system, making it easier to integrate into your project without compromising on safety or strength.
Design Principles for Buckling Restrained Braced Frames
Designing a Buckling Restrained Braced Frame goes beyond crunching numbers. It’s about creating a system that blends safety, functionality, and cost-efficiency.
Each design is tailored to meet the unique needs of the project. At its heart, it’s a thoughtful process grounded in understanding structural behavior and environmental demands.
Start with the Big Picture: Understanding the Building’s Environment
Every great design begins with asking the right questions:
- Is the building in an earthquake zone? If so, how intense are the expected seismic forces?
- What’s the natural vibration period of the structure?
- Are wind or seismic forces the bigger challenge? In wind-heavy regions, for instance, lateral resistance might focus on wind loads over earthquake performance.
These considerations lay the groundwork for choosing the right system. And when earthquakes are a major concern, BRBFs are the clear winner most of the time.
Tailoring BRBFs to Fit Your Structure
Once you’ve decided on BRBFs, it’s time to make them work for your building. This isn’t a one-size-fits-all approach—it’s about customization:
- Retrofitting an older structure? Narrow, lightweight braces fit seamlessly into existing walls without tearing everything apart. (Like our all-steel EVER braces)
- Need minimal disruption? Lightweight braces—like EVER’s all-steel designs—are easier to lift, maneuver, and install. Perfect for projects like hospitals or schools where operations can’t pause.
And of course, there are the material, weight, and cost considerations. Choosing between traditional concrete-filled braces and lighter all-steel options can significantly impact your project budget.
Cost-Efficiency Beyond the Brace
With BRBFs costs go beyond the brace itself. The real savings come from looking at the whole system:
- Connections and Gusset Plates: The way braces connect to your structure significantly affects pricing. Well-designed gussets keep costs down and performance up.
- Installation: Lightweight braces don’t just simplify installation—they cut down labor and equipment costs, too.
Design Challenges? We’ve Got Solutions
Designing BRBFs comes with its share of hurdles, especially when it comes to connections. Missteps here can lead to higher costs—or worse, compromised safety.
That’s why collaboration is key.
Early input from manufacturers and engineers ensures everything clicks into place, literally and figuratively.
Imagine this scenario: A hospital plans to add two additional stories. Minimizing disruption to daily operations is critical. By selecting a lighter all-steel BRBF, the project benefits from:
- Ease of Installation: A lighter brace means smaller cranes can handle the lift, significantly reducing equipment costs.
- Reduced Structural Load: By leveraging a reduced acceleration spectrum, BRBFs minimize seismic loads on the structure.
- Cost and Operational Efficiency: With a more streamlined installation process, facilities like hospitals can remain partially operational, avoiding the financial impact of a full shutdown.
Designing a BRBF is about more than just meeting seismic codes; it’s about creating a smarter, more efficient system that delivers on every front. With thoughtful choices and innovative solutions, you’re not just building a structure—you’re building resilience.
Common Sizes and Configurations for Buckling Restrained Braced Frames
With BRBFs flexibility is key.
They aren’t a one-size-fits-all solution.
From retrofits to skyscrapers, their sizes and configurations adapt to the unique demands of each project.
Let’s break down how it all works.
How Are Brace Sizes Calculated?
Sizing a brace starts with understanding the building itself.
What kind of forces are we dealing with?
Engineers calculate the required force to handle the load, and manufacturers step in to craft a brace that meets the required area, force, or the required stiffness.
Four Factors That Shape a Buckling Restrained Brace
Every BRBF is unique, but its size comes down to a few core considerations:
- The load and area of the building.
- The structure’s behavior and size.
- The building’s location.
- The period (resonance) of the building.
These factors determine not only the size of the brace but also how it interacts with the structure.
BRBF Sizes – From Small to Mighty
BRBFs range from compact 2-square-inch braces to colossal 40-square-inch giants.
For specific scenarios, engineers might opt for two smaller braces instead of a single oversized one—keeping the balance just right. And yes, testing those massive braces requires specialized facilities, like the high-tech labs in Taiwan.
How Are Buckling Restrained Braces Tested?
Testing BRBs is about ensuring they deliver reliable, seismic performance. Here’s how it works:
There Are Two Key Tests
- Brace Test: This focuses solely on the brace itself, putting it through cycles of pushing and pulling to see how it performs on its own.
- Brace Assembly Test: This evaluates how the brace, gusset, and connections work together, testing the full system under pressure.
Both tests adhere to strict seismic code requirements, including specific load thresholds and strains.
After code requirements are met, manufacturers often push their braces to the edge, simulating worst-case scenarios. Only successful tests are allowed to be used in building design. Engineers can be assured what brace they require has passed live testing multiple times.
Then Peer Reviews for Accountability Follows
Testing must be done by an independent lab and go through a rigorous review process. Manufacturers must design braces that align with the tested performance, ensuring consistency and dependability.
Cost Factors for Buckling Restrained Braced Frames
Let’s talk about what goes into the cost of buckling restrained braced frames and how they can actually help optimize your project budget.
What Drives the Cost?
Four key factors influence BRBF pricing:
- Design: All EVER BRBs are designed by specialized EVER engineers, ensuring they meet design specifications and testing standards
- Materials: There are a variety of steel parts in the brace. Fluctuating market price can directly impact costs.
- Labor: Manufacturing and assembling BRBss done in a certified shop.
- Shipping: Moving these components to your site is another piece of the puzzle.
How BRBFs Help Save Costs
Here’s where the magic of BRBFs comes in—they’re not just about safety; they’re also smart for your budget. By reducing the seismic load on foundations, beams, and columns, BRBFs allow for smaller, more affordable structural components.
At EVER Seismic, we go a step further. We meticulously design connections for every project, improving performance and cutting down on material and fabrication costs.
The result?
A system that’s as efficient as it is resilient.
Tips to Maximize Value
- Go Lighter with All-Steel: All-steel designs are not only easier to ship and install but also reduce overall building costs without compromising strength.
- Choose a Trusted Partner: A knowledgeable partner can refine the design to fit your needs—no unnecessary costs and extras, just optimized performance.
Applications of Buckling Restrained Braced Frames
BRBFs are versatile structural solutions that shine in projects requiring exceptional lateral load resistance. There are many applications for the buckling restrained brace. Here’s where they’re making a significant impact:
1. High-Rise Buildings
In tall structures, managing seismic forces efficiently is a priority. BRBFs handle these forces while allowing for slender and space-saving designs, making them a cornerstone of urban high-rises.
2. Warehouses and Data Centers
These facilities often house valuable and sensitive equipment. BRBFs provide reliable seismic protection, ensuring safety without overcomplicating the design or increasing costs unnecessarily.
3. Hospitals and Schools
Safety and resilience are critical in these environments. BRBFs offer the structural strength needed to withstand earthquakes while maintaining cost-efficiency and minimizing disruption during construction or retrofits.
4. Airports
Airports often use BRBFs in terminal designs, where their visible structures enhance aesthetics while providing robust seismic resistance.
5. Retrofitting Projects
For older brick or concrete buildings, BRBFs are an effective solution for meeting modern seismic codes. Their adaptability allows them to fit within existing walls or structural constraints with minimal disruption.
Whether it’s a bustling airport terminal or a historic building upgrade, BRBFs prove time and again that they’re more than just braces—they’re integral to resilient and innovative design.
What to Look for in a Manufacturer and Supplier of BRBFs
Choosing the right partner for your buckling restrained braced frames can make or break your project. With multiple buckling restrained brace manufacturers and suppliers in the market, knowing what matters most will guide you to the best fit. Here’s what to keep in mind when evaluating buckling restrained brace suppliers and their offerings:
1. Quality Standards and Certifications
Your first checkpoint? Certifications.
Reliable manufacturers will openly share details about their seismic code compliance, rigorous testing processes, and peer reviews. Look for those who not only meet industry standards but consistently exceed them.
2. Expertise and Proven Experience
Experience brings foresight.
A trusted supplier will have a history of successful projects and diverse applications. Don’t hesitate to ask for project examples and references to gauge their expertise and reliability.
3. Design Precision and Optimization
A great manufacturer isn’t just about delivering braces; they contribute to better project outcomes.
At EVER Seismic, for example, we prioritize refining every detail, from brace connections to custom designs, to reduce costs and enhance performance.
4. Seamless Coordination and Installation
How well does the supplier’s process integrate with your team’s?
Look for manufacturers who offer detailed drawings, easy-to-install products, and responsive support. Smooth coordination with contractors and engineers keeps your project moving without unnecessary headaches.
5. Innovation and Adaptability
Innovation separates good from great.
Suppliers offering advanced solutions—like lightweight all-steel BRBFs—bring benefits like faster installation, reduced crane requirements, and better sustainability. Make sure your supplier can adapt their products to fit your project’s unique needs.
6. Timely Delivery and Ongoing Support
Delays are costly.
Choose a manufacturer known for on-time delivery and a commitment to supporting your project beyond installation. Reliability here ensures your timeline stays intact.
The Bottom Line
Your BRBF supplier isn’t just providing a product; they’re a partner in your project’s success. Look for quality, experience, innovation, and dependability. With the right manufacturer, your BRBFs won’t just meet expectations—they’ll exceed them.
Red Flags to Watch for When Choosing a BRBF Supplier
Now you know what to look for in a buckling restrained brace manufacturer. But what are the red flags that signal you might be headed for trouble? Choosing the wrong supplier can result in delays, costly adjustments, and unnecessary stress. Here’s what to keep on your radar:
1. Negative Feedback from Past Clients
Pay attention to what others have experienced with the supplier. Common complaints include:
- Braces That Don’t Fit: Precision is everything. Misaligned or improperly sized braces can throw off your entire project schedule.
- Delivery Delays: Braces that arrive late can cause serious disruptions, especially on tight timelines.
2. Poor Coordination and Communication
A great supplier will work seamlessly with your team. Red flags to watch for:
- Lack of clear instructions or detailed plans.
- Inability to adapt to your project’s unique requirements.
- Slow or unclear communication during the first phases.
Unfortunately, some issues only become apparent once work is underway. That’s why doing your homework upfront is critical. Ask for references, dig into past projects, and evaluate the supplier’s responsiveness from the start.
The bottom line? Don’t just settle for a product—choose a partner you can trust to make your project a success.
Common Mistakes When Selecting or Designing BRBFs
Mistakes in choosing or designing buckling restrained braced frames can cause headaches you don’t need. Let’s look at where things often go wrong—and how to avoid them.
1. Over-Specifying Engineering Details
Sometimes engineers get too specific, and while it’s well-intentioned, it can backfire. Examples?
- Gusset Thickness Overload: Setting minimum gusset sizes that don’t align with the manufacturer’s best practices.
- Connection Micromanagement: Designing rigid connections that prevent manufacturers from finding cost-efficient solutions.
How You Fix It: Bring in the BRBF manufacturer early. Their expertise can help streamline designs while saving you time and money.
2. Waiting Too Long to Involve the Manufacturer
Postponing manufacturer input? Big mistake.
When they’re brought in late, you miss out on:
- Smart Suggestions: Cost-effective brace configurations or installation hacks.
- Connection Optimizations: Designs that save labor, materials, and ultimately costs.
- Optimizing the Beam/Columns/Footings: When using BRBFs these members can often be smaller. Knowing your BRBF parameters ahead of time can help you design the other members.
3. Picking the Wrong Manufacturer
As I said before, an unreliable manufacturer can cause trouble, like:
- Missed Requirements: Products that don’t meet technical standards.
- Delivery Delays: Braces that don’t show up when you need them.
Avoid It: Do your homework. Choose a manufacturer with a solid track record and glowing reviews from past clients.
How to Get it Right
The secret?
Early collaboration.
Partnering with your BRBF manufacturer from the start ensures designs that work, materials that perform, and solutions that fit your project like a glove.
The Future of Buckling Restrained Braced Frames
What’s next for seismic innovation?
BRBFs are already redefining how we approach structural safety, but their evolution is far from over.
This is what we think the future holds:
- All-Steel Braces Taking the Lead: Lightweight, recyclable, and easy to install, all-steel designs are set to become the industry standard, led by pioneers like EVER Seismic.
- Rising Adoption in Construction: Growing awareness and integration into building codes make BRBFs a go-to for high-rises, warehouses, and more.
- Smaller-Scale Applications Emerging: Beyond construction, BRBFs could stabilize precision instruments and sensitive equipment, expanding their reach into fields like healthcare and tech.
As technology advances and education spreads, BRBFs are poised to revolutionize industries far beyond construction, setting new benchmarks for safety and versatility.
BRBFs – Building Resilience, One Brace at a Time
At the heart of every structure lies a commitment to safety and adaptability. Buckling restrained braced frames (BRBFs) (especially all-steel ones) represent more than just a technological leap; they embody a mindset shift—one that prioritizes performance and precision over outdated limitations.
Two key lessons stand out:
- BRBFs aren’t just about enduring seismic forces; they’re about transforming those forces into manageable energy.
- And secondly, the choice of innovative, well-designed components, like all-steel braces, can redefine what’s possible in both cost efficiency and structural resilience.
The next time the ground moves, will your structure stand as a testament to innovation? With BRBFs, the answer isn’t just “yes”—it’s “let’s move forward.”